Propiedades generales
La aleación 625 (UNS N06600) es una aleación austenítica de níquel-cromo-molibdeno-niobio que ofrece una combinación única de excepcional resistencia a la corrosión y alta resistencia en un amplio rango de temperaturas. La resistencia de la aleación 625 se logra mediante el endurecimiento en solución sólida de la matriz de níquel-cromo por la presencia de molibdeno y niobio. Esto elimina la necesidad de tratamientos de endurecimiento por precipitación, lo que simplifica el proceso de fabricación. La composición química de la aleación 625 contribuye a su excelente resistencia a la corrosión en diversos entornos operativos severos. También exhibe resistencia a la oxidación y carburación a altas temperaturas. La aleación demuestra resistencia a la corrosión por picaduras, corrosión por grietas, corrosión por impacto y ataque intergranular. Además, es altamente resistente al agrietamiento por corrosión bajo tensión por cloróxido, lo que lo hace casi inmune a esta forma de corrosión.
La aleación 625, la excepcional resistencia a la corrosión y la alta resistencia la hacen adecuada para una amplia gama de aplicaciones. Se usa comúnmente en industrias como el procesamiento químico, el petróleo y el gas, la ingeniería marina, la industria aeroespacial y la generación de energía. La aleación es adecuada para entornos donde se espera exposición a medios corrosivos, temperaturas elevadas y tensiones mecánicas.
Aplicaciones
- Componentes aeroespaciales: fuelles y juntas de expansión, sistemas de conductos, inversores de empuje del motor, anillos de cubierta de turbina
- Control de la contaminación del aire: revestimientos de chimeneas, compuertas, componentes de desulfuración de gases de combustión (FGD)
- Procesamiento químico: equipos que manejan ácidos oxidantes y reductores, producción de ácido superfosfórico
- Servicio Marítimo: fuelles de líneas de vapor, sistemas de escape de buques de la Armada, sistemas de propulsión auxiliares de submarinos
- Industria nuclear: componentes del núcleo del reactor y de la barra de control, equipos de reprocesamiento de residuos
- Producción de petróleo y gas en alta mar: chimeneas de gas de antorcha residual, sistemas de tuberías, revestimiento de elevadores, tuberías y tubos de gas ácido
- Refinación de petróleo: chimeneas de gas de combustión residual
- Tratamiento de residuos: componentes de incineración de residuos
Normas
ASTM.................. B 443ASME.................. SB 443
AMS................... 5599
Análisis químico
% de peso (todos los valores son máximos a menos que se indique lo contrario en un rango)
|
|
|
|
Níquel |
58.0 min. |
Silicio |
0.50 |
Cromo |
20.0 mín.-23.0 máx. |
Fósforo |
0.015 |
Molibdeno |
8.0 mín.-10.0 máx. |
Azufre |
0.015 |
Hierro |
5.0 |
Aluminio |
0.40 |
Niobio (más tantalio) |
3.15 min.-4.15 máx. |
Titanio |
0.40 |
Carbono |
0.10 |
Cobalto (si se determina) |
1.0 |
Manganeso |
0.50 |
|
|
Propiedades físicas
Densidad
0.305 libras/pulg.38,44 g/cm3
Calor específico
0.102 BTU/lb-°F (32-212°F)427 J/kg-°K (0-100°C)
Módulo de elasticidad
30,1 x 106 psi207.5 GPa
Conductividad térmica 200 °F (100 °C)
75 BTU/hr/ft2/ft/°F10,8 W/m-°K
Rango de fusión
2350 – 2460 °F1290 – 1350°C
Resistividad eléctrica
50,8 microhm-in a 70 °C128,9 microhm-cm a 210 °C
Coeficiente medio de dilatación térmica |
|||
°F |
°C |
pulgadas/pulgadas/°F |
cm/cm°C |
200 |
93 |
7.1 x 10-6 |
12,8 x 10-6 |
400 |
204 |
7,3 x 10-6 |
13,1 x 10-6 |
600 |
316 |
7,4 x 10-6 |
13,3 x 10-6 |
800 |
427 |
7,6 x 10-6 |
13,7 x 10-6 |
1000 |
538 |
7,8 x 10-6 |
14.0 x 10-6 |
1200 |
649 |
8,2 x 10-6 |
14,8 x 10-6 |
1400 |
760 |
8,5 x 10-6 |
15,3 x 10-6 |
1600 |
871 |
8,8 x 10-6 |
15,8 x 10-6 |
1700 |
927 |
9.0 x 10-6 |
16,2 x 10-6 |
Propiedades mecánicas
Valores típicos a 68 °F (20 °C)
Límite elástico |
Tracción máxima |
Alargamiento |
Dureza |
||
psi (mín.) |
(MPa) |
psi (mín.) |
(MPa) |
% (mín.) |
(máx.) |
65,000 |
448 |
125,000 |
862 |
50 |
200 Brinell |
Resistencia a la corrosión
La composición química altamente aleada de la aleación 625 proporciona una excelente resistencia a la corrosión en diversos entornos severamente corrosivos. Estos son algunos puntos clave sobre la resistencia a la corrosión de la aleación 625:Inmunidad al ataque en condiciones suaves:La aleación 625 es prácticamente inmune al ataque en condiciones suaves como la atmósfera, el agua dulce y de mar, las sales neutras y las soluciones alcalinas. El níquel y el cromo en la aleación contribuyen a su resistencia a las soluciones oxidantes. La combinación de níquel y molibdeno ofrece resistencia en ambientes no oxidantes. Resistencia a la corrosión por picaduras y grietas: La aleación 625 es resistente a la corrosión por picaduras, que es la corrosión localizada que puede causar pequeños agujeros o hoyos en la superficie del material. También resiste la corrosión por grietas, que se produce en espacios confinados o grietas. Prevención del agrietamiento intergranular: El niobio, presente en la aleación 625, actúa como estabilizador durante la soldadura, evitando el agrietamiento intergranular. El agrietamiento intergranular puede ocurrir a lo largo de los límites de los granos metálicos durante la soldadura. Inmunidad al agrietamiento por corrosión bajo tensión por cloruro: El alto contenido de níquel de la aleación 625 lo hace prácticamente inmune al agrietamiento por corrosión bajo tensión por cloruro. El agrietamiento por corrosión bajo tensión por cloruro es un tipo de corrosión que se produce en presencia de cloruros y tensión de tracción. Resistencia a ácidos minerales, álcalis y ácidos orgánicos: La aleación 625 resiste el ataque de ácidos minerales como los ácidos clorhídrico, nítrico, fosfórico y sulfúrico. También muestra resistencia a los álcalis y ácidos orgánicos tanto en condiciones oxidantes como reductoras.
La resistencia a la corrosión de la aleación 625 permite su uso en una amplia gama de aplicaciones en las que se espera la exposición a entornos hostiles y sustancias corrosivas. Sin embargo, es importante tener en cuenta las condiciones de funcionamiento específicas y consultar con ingenieros de materiales o fabricantes de aleaciones para garantizar la idoneidad de la aleación para una aplicación concreta.
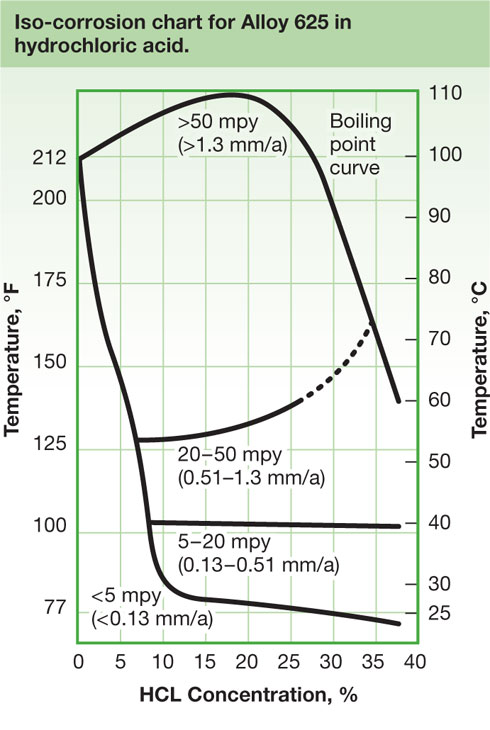

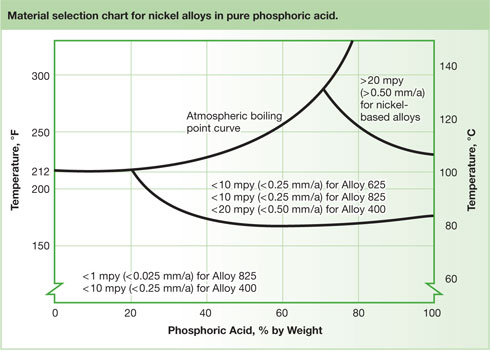
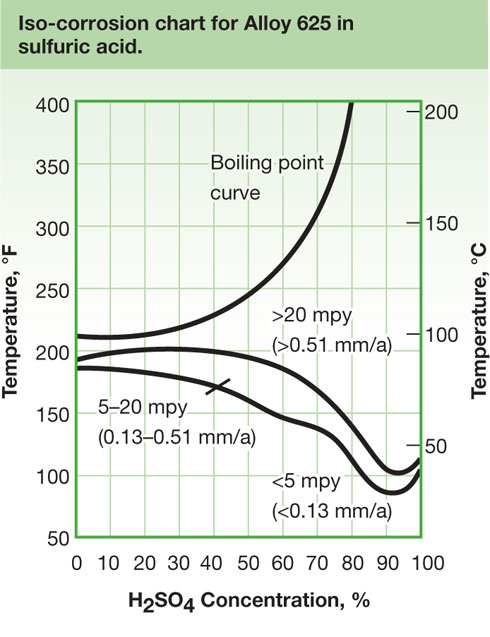
Aleación |
Velocidad de corrosión |
|
|
mpy |
mm/a |
Aleación 825 |
7.9 |
0.2 |
Níquel 200 |
10.3-10.5 |
0.26-0.27 |
Aleación 400 |
1.5-2.7 |
0.038-0.068 |
Aleación 600 |
10.0 |
0.25 |
Aleación G-3 |
1.8-2.1 |
0.046-0.05 |
Aleación 625 |
6.8-7.8 |
0.17-0.19 |
Aleación C-276 |
2.8-2.9 |
0.07-0.074 |
Resistencia a la corrosión de aleaciones de níquel en cuatro pruebas de 24 horas en ácido acético hirviendo
Aleación |
Ácido acético |
Tasa de corrosión/erosión |
|
mpy |
mm/a |
||
Aleación 825 |
10% |
0.60-0.63 |
0.0152-0.160 |
Aleación 625 |
10% |
0.39-0.77 |
0.01-0.19 |
Aleación C-276 |
10% |
0.41-0.45 |
0.011-0.0114 |
Aleación 686 |
80% |
<0,1* |
<0,01* |
Resistencia de las aleaciones de níquel al ataque de impacto del agua de mar a 150 pies/seg (45,7 m/s)
Aleación |
Tasa de corrosión/erosión |
|
|
mpy |
mm/a |
Aleación 625 |
Cero |
Cero |
Aleación 825 |
0.3 |
0.008 |
Aleación K-500 |
0.04 |
0.01 |
Aleación 400 |
1.5-2.7 |
0.038-0.068 |
Aleación 600 |
0.4 |
0.01 |
Níquel 200 |
40 |
1.0 |
El número PREN comparativo para la aleación 625 se muestra en la siguiente tabla.
Números de equivalencia de resistencia a picaduras (PREN) para aleaciones resistentes a la corrosión
Aleación |
Ni |
Cr |
Mo |
W |
Nb |
N |
PREN |
Acero inoxidable 316 |
12 |
17 |
2.2 |
— |
— |
— |
20.4 |
Acero inoxidable 317 |
13 |
18 |
3.8 |
— |
— |
— |
23.7 |
Aleación 825 |
42 |
21.5 |
3 |
— |
— |
— |
26.0 |
Aleación 864 |
34 |
21 |
4.3 |
— |
— |
— |
27.4 |
Aleación G-3 |
44 |
22 |
7 |
— |
— |
— |
32.5 |
Aleación 625 |
62 |
22 |
9 |
— |
3.5 |
— |
40.8 |
Aleación C-276 |
58 |
16 |
16 |
3.5 |
— |
— |
45.2 |
Aleación 622 |
60 |
20.5 |
14 |
3.5 |
— |
— |
46.8 |
SSC-6MO |
24 |
21 |
6.2 |
— |
— |
0.22 |
48.0 |
Aleación 686 |
58 |
20.5 |
16.3 |
3.5 |
— |
— |
50.8 |
Resistencia a la oxidación
La resistencia a la oxidación y a las incrustaciones de la aleación 625 es superior a una serie de aceros inoxidables austeníticos resistentes al calor, como 304, 309, 310 y 347, hasta 1800 °F (982 °C) y en condiciones cíclicas de calentamiento y enfriamiento. Por encima de 1800 °F (982 °C), las incrustaciones pueden convertirse en un factor restrictivo en el servicio.
Datos de fabricación
La aleación 625 se puede soldar y procesar fácilmente mediante las prácticas estándar de fabricación en taller, sin embargo, debido a la alta resistencia de la aleación, resiste la deformación a temperaturas de trabajo en caliente.
Conformado en caliente
El rango de temperatura de trabajo en caliente para la aleación 625 es de 1650 a 2150 °F (900 a 1177 °C). El trabajo pesado debe realizarse lo más cerca posible de 2150 ° F (1177 ° C), mientras que el trabajo más ligero puede tener lugar hasta 1700 ° F (927 ° C). El trabajo en caliente debe realizarse en reducciones uniformes para evitar la estructura de grano dúplex
La aleación 400 se trabaja fácilmente en frío mediante prácticamente todos los métodos de fabricación en frío. El trabajo en frío debe realizarse en material recocido. La aleación tiene una tasa de endurecimiento por trabajo algo más alta que el acero al carbono, pero no tan alta como el acero inoxidable 304.
Conformado en frío
La aleación 625 se puede conformar en frío mediante las prácticas estándar de fabricación en taller. La aleación debe estar en estado recocido. Las tasas de endurecimiento por trabajo son más altas que las de los aceros inoxidables austeníticos.
Soldadura
La aleación 625 se puede soldar fácilmente mediante la mayoría de los procesos estándar, incluidos GTAW (TIG), PLASMA, GMAW (MIG / MAG), SAW y SMAW (MMA). No es necesario un tratamiento térmico posterior a la soldadura. El cepillado con un cepillo de alambre de acero inoxidable después de la soldadura eliminará el tinte térmico y producirá un área de superficie que no requiere decapado adicional.
Mecanizado
La aleación 625 debe mecanizarse preferiblemente en estado recocido. Dado que la aleación 625 es propensa al endurecimiento por trabajo, solo se deben usar velocidades de corte bajas y la herramienta de corte debe estar activada en todo momento. Es necesaria una profundidad de corte adecuada para asegurar que se evite el contacto con la zona endurecida previamente formada.